welding to the block
#1

I have a pretty good question i hope, i was wondering if anyone could help me with an answer. I dropped the bike about 2 months ago and my stator cover just broke that was all and all the oil came out so am guessing thats why it wouldnt turn on cause of safety mode came on am i correct?.... also i recently got a new stator cover and i was trying to replace the old with the new one and was i was unscrewing one of the bolts and a lil chunck on the side where you can screw on the stator was broken off i got the lil chunk i was wondering if its safe to weld that lil chunk back on to the block so i can be able to screw the stator back on and so it wont leak oil out of there, and am asking is all i have todo is remove the battery from the bike so the wiring wont get messed up because its being welded on, the strong current running through there wont mess up the wiring am i correct? Please if anyone can please help with my question? i hope i was detailed enough

#3
#4

If you decide to weld it then it is important to unhook the battery. You dont have to worry about any of the electronics, as long as the battery is disconnected. As for welding, not too sure about aluminum, but with cast iron (the motor is cast aluminum) you have to arc weld it with a special rod, if you try to weld it via mig or tig the material just melts away (again thats regular ol' steel thats been "cast") However you decide to fix it, you need to thread the bolt in BEFORE you make it permanent. (i.e. the JB sets or you strike an arc) Good luck.
#5

here are the pieces that broke of the block and i was asking you guys about wats the best way to go to try to fix the problem, i have posted up pics to you guys how big and what piece it is
this is the first picture thats how big the piece its not really big at all but it goes to the block
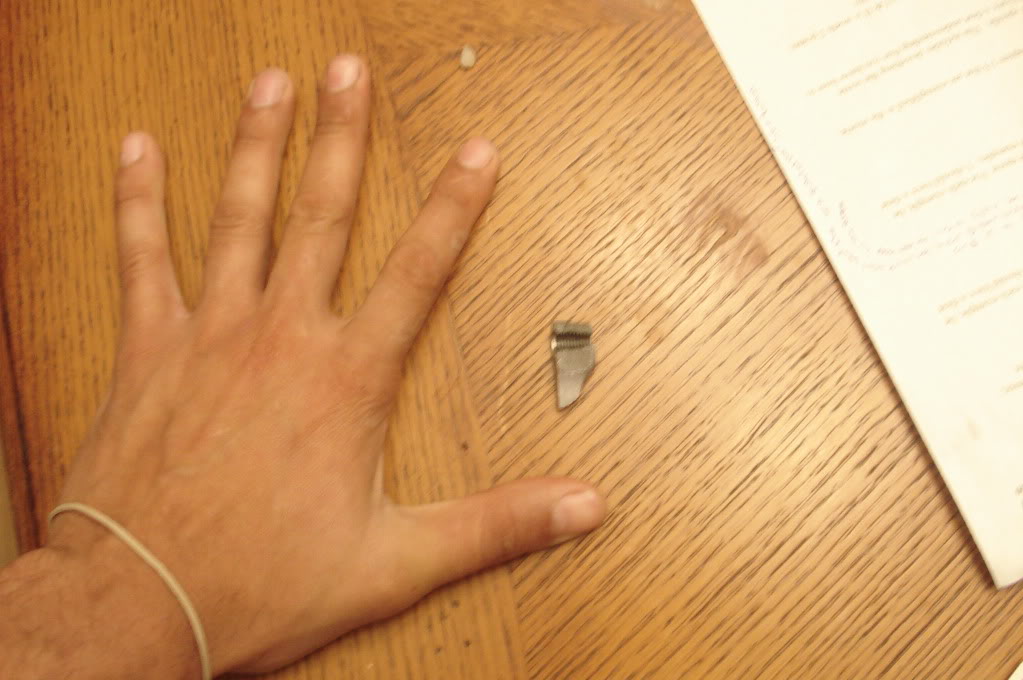
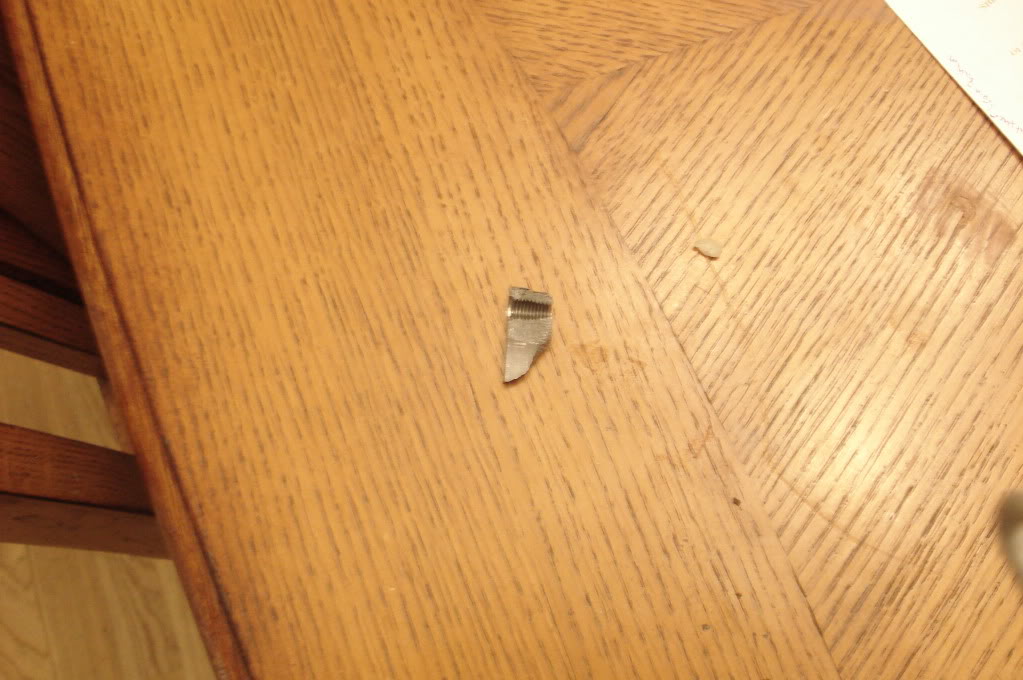
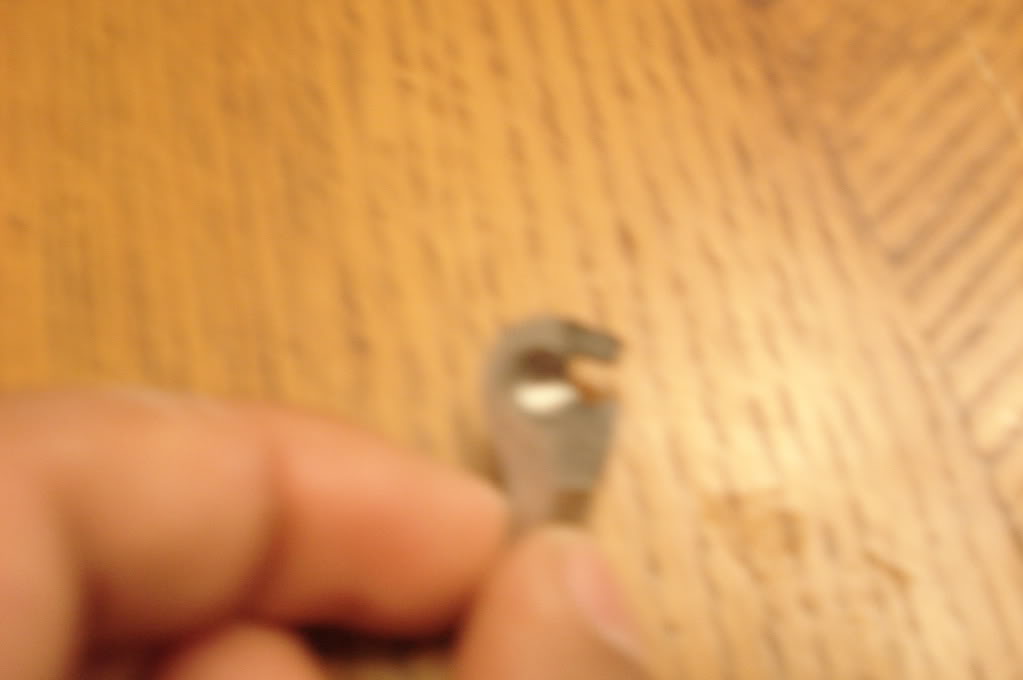
This little piece am holding to the block where the screw screws in am holding it in place
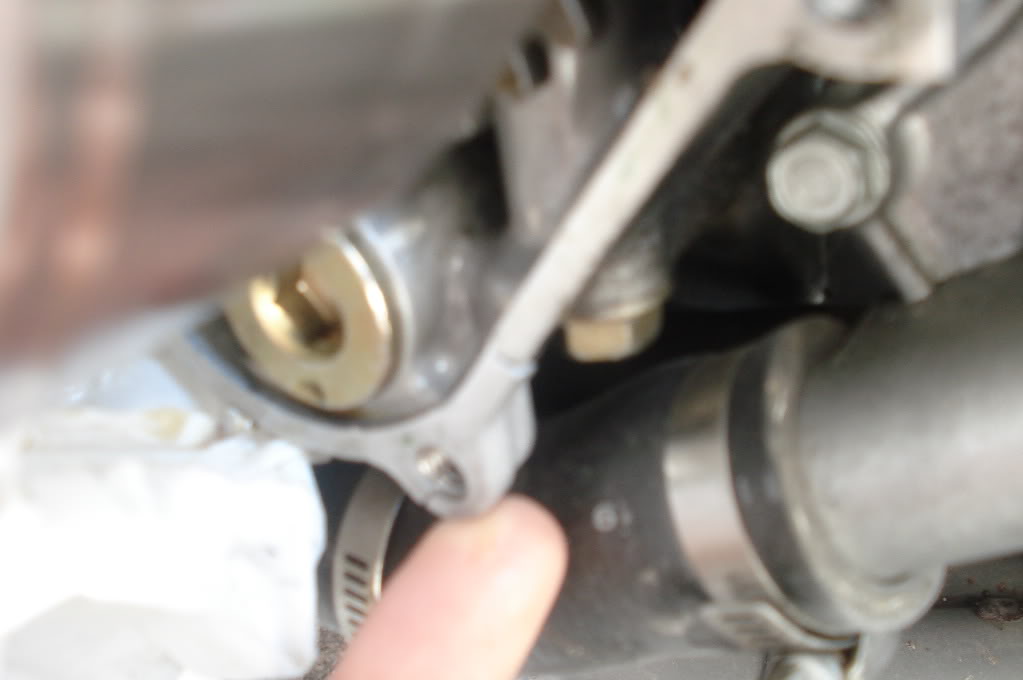
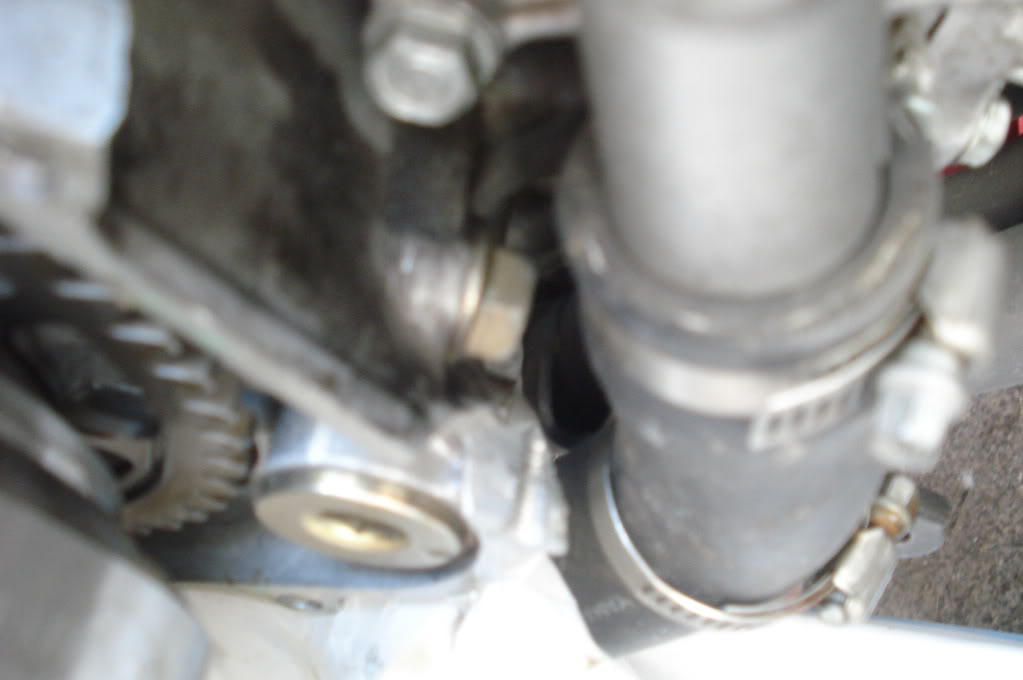
this is the first picture thats how big the piece its not really big at all but it goes to the block
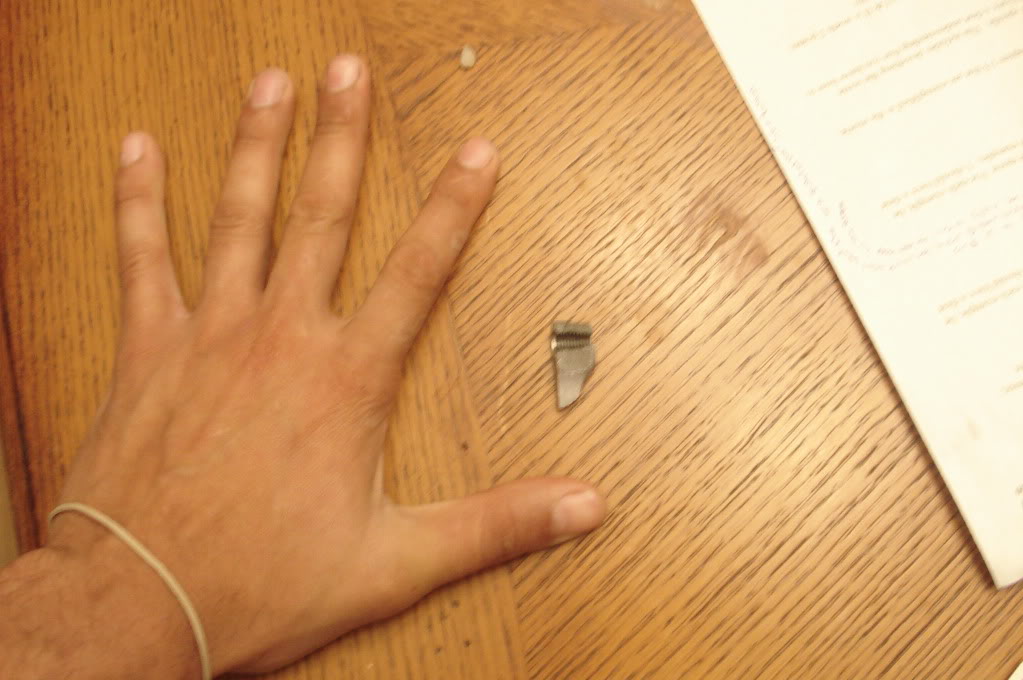
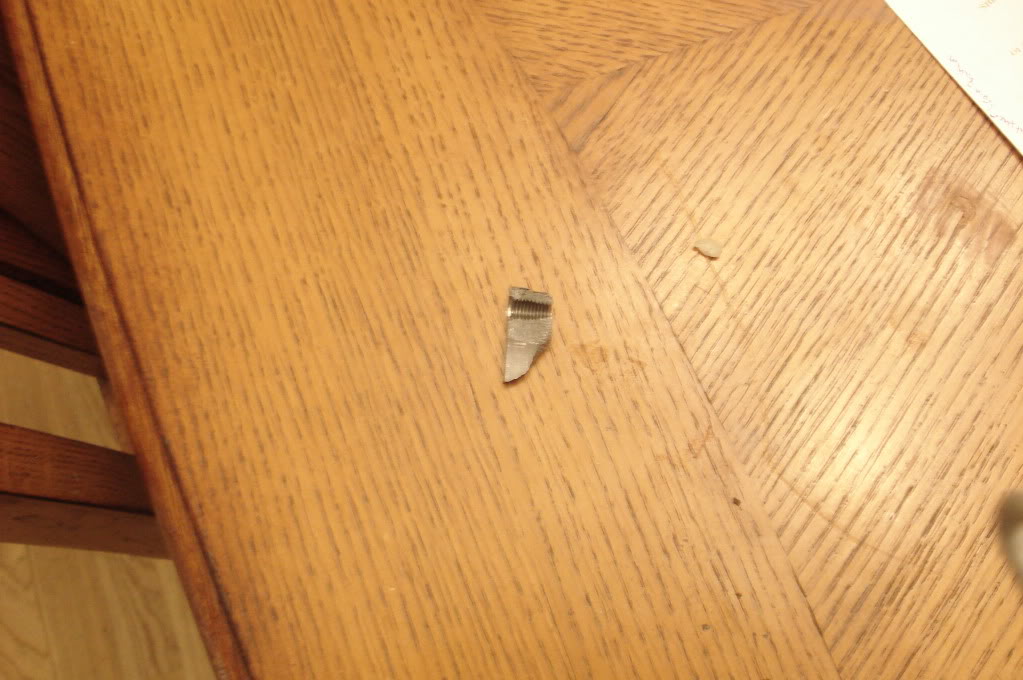
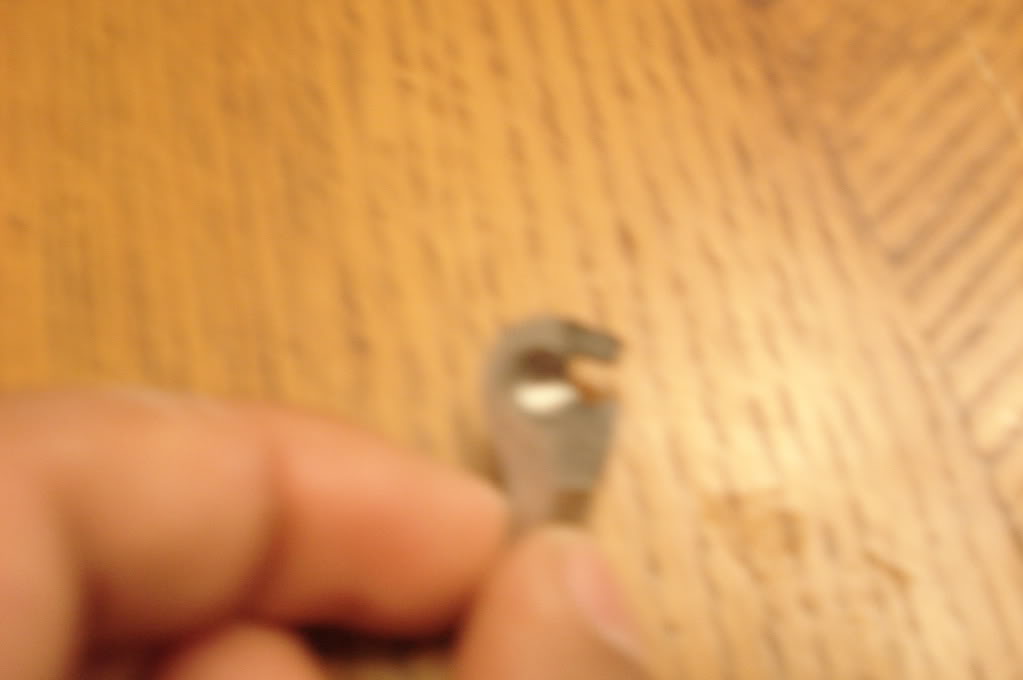
This little piece am holding to the block where the screw screws in am holding it in place
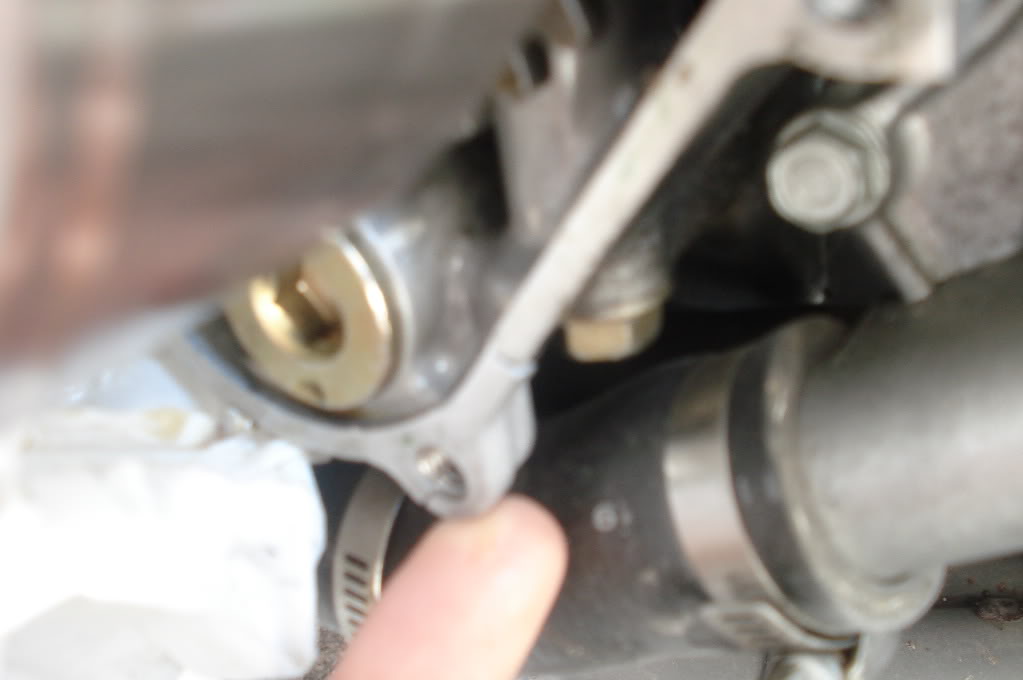
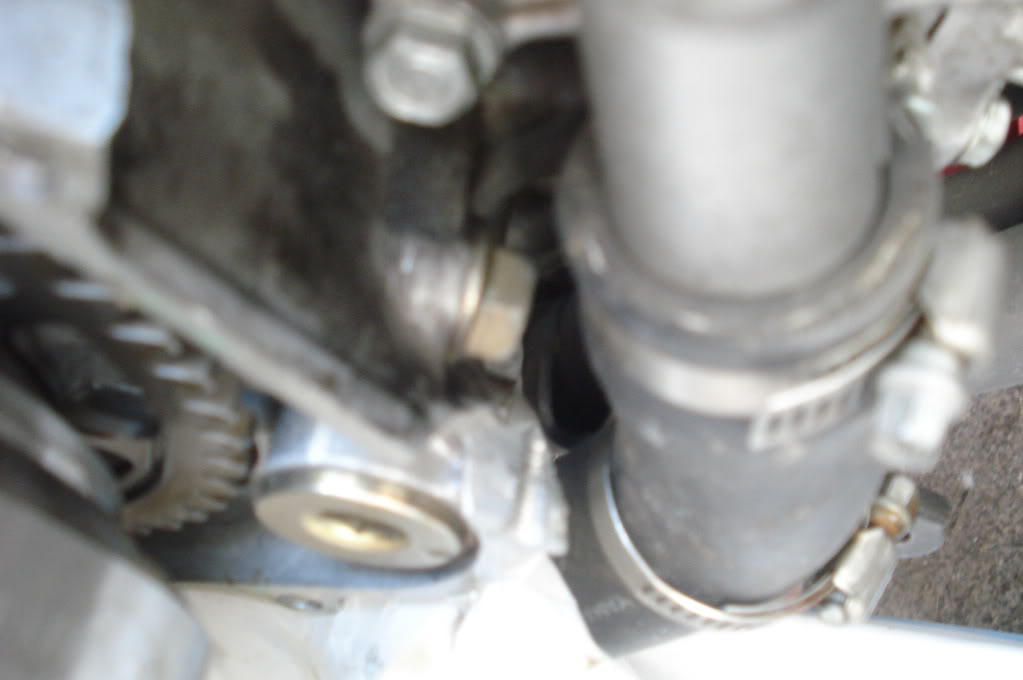
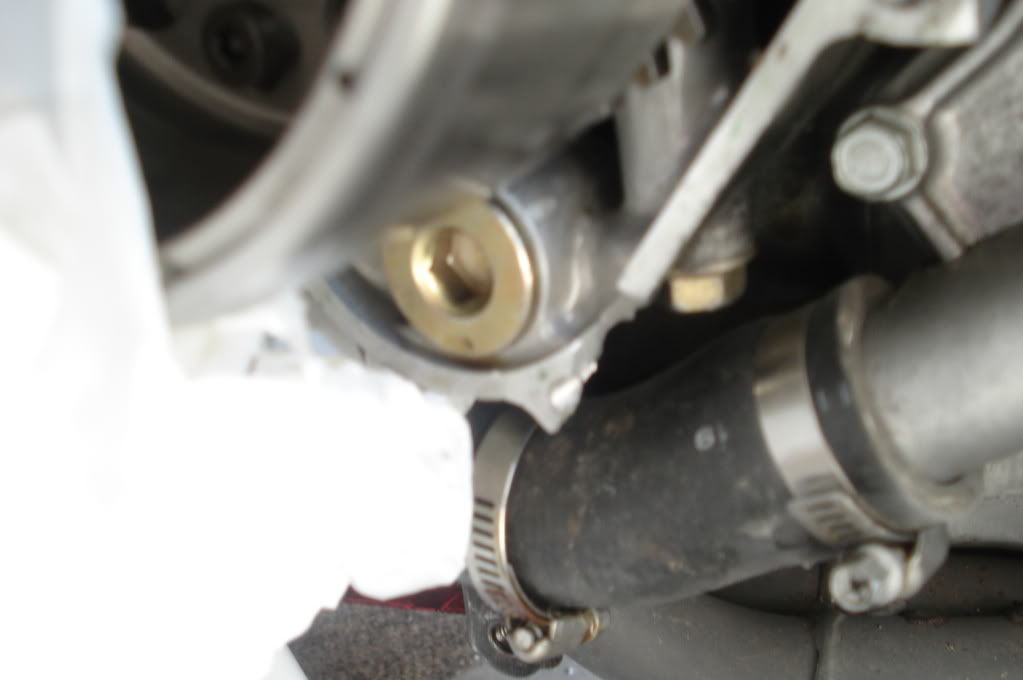
Last edited by 01niceF4i; 03-23-2009 at 12:29 PM.
#6
#7

Don't JB weld it. If you want it to last for any length of time, weld it for real real. And by weld it for real real, I mean take it to a shop and have someone who welds for a living do it for you. Shouldn't cost more than $25 or so, and you have the piece of mind knowing that it's not going to fall off while you ride down the road like it would with JB weld.
You'll most likely have to redrill and tap that hole, and will have to take some extra time with a fine file and a metal straight edge to make the sealing surface straight again (so it seals), but you might as well do it right if you're going to do it at all.
BTW- for better close up pictures, keep the camera a few feet away from the subject matter and use the zoom to get close.
You'll most likely have to redrill and tap that hole, and will have to take some extra time with a fine file and a metal straight edge to make the sealing surface straight again (so it seals), but you might as well do it right if you're going to do it at all.
BTW- for better close up pictures, keep the camera a few feet away from the subject matter and use the zoom to get close.
#8

[QUOTE=Luck Runs Out...;761244]
You'll most likely have to redrill and tap that hole, and will have to take some extra time with a fine file and a metal straight edge to make the sealing surface straight again. [QUOTE]
This why I said use the bolt, so you wont have to retap the hole. But you might have to file it a little.
You'll most likely have to redrill and tap that hole, and will have to take some extra time with a fine file and a metal straight edge to make the sealing surface straight again. [QUOTE]
This why I said use the bolt, so you wont have to retap the hole. But you might have to file it a little.
#9

The problem with that is keeping the piece aligned exactly while welding. I didn't mean fill the hole, but because of its shape, it's going to be very hard to stabilize during the heating cycle of welding. The piece WILL shift and warp slightly, so retapping WILL be needed. Welding with the bolt in the hole could very well still cause the piece to shift since steel expands faster than aluminum and because of its proximity to the weld, will be heated to the same temp as the aluminum.
Also, your statement about MIG or TIG just melting the material away is misleading. That's like saying don't use tires on the bike; they just wear off. Of course there's going to be slight material consumption; that's one of the reasons why a filler rod is used. Adjust your heat accordingly and there will be negligable losses before the filler is added. Either MIG or TIG would be perfectly acceptable if done right, as any professional will be able to. If it were a structural part, I'd say TIG, but since it's not, MIG would be perfectly fine.
Like I said... take it to a shop and let them deal with the details.
Also, your statement about MIG or TIG just melting the material away is misleading. That's like saying don't use tires on the bike; they just wear off. Of course there's going to be slight material consumption; that's one of the reasons why a filler rod is used. Adjust your heat accordingly and there will be negligable losses before the filler is added. Either MIG or TIG would be perfectly acceptable if done right, as any professional will be able to. If it were a structural part, I'd say TIG, but since it's not, MIG would be perfectly fine.
Like I said... take it to a shop and let them deal with the details.

#10

Ya, i had the same problem and all i just had to use a low heat aluminum weld/braze. Low heat just means heat under a propane torch, non flux heat. I got this stuff called Alumoaloy but there are tons of other brazing rods that do the same thing. Just make sure to get the aluminum nice and HOT! Trust me and take your time, if you do it right you will not have a prob.
Here r some other low heat aluminum rods,
http://durafix.com/index.html
http://www.alumaloy.net
http://weld-aluminum.com
Videos
http://www.youtube.com/watch?v=jijW310xvp4
http://www.youtube.com/watch?v=mMADiAMfe00
Here r some other low heat aluminum rods,
http://durafix.com/index.html
http://www.alumaloy.net
http://weld-aluminum.com
Videos
http://www.youtube.com/watch?v=jijW310xvp4
http://www.youtube.com/watch?v=mMADiAMfe00